The Proving Grounds
The Proving Grounds
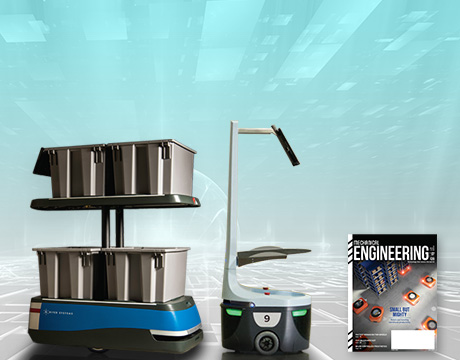
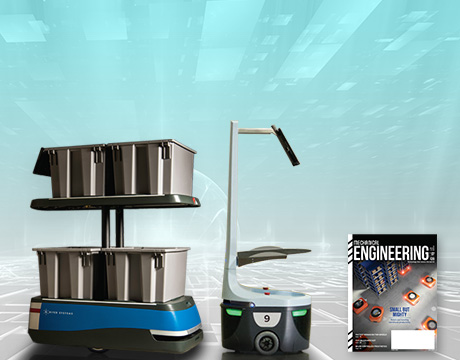
Bruce Welty would never have entered the robotics industry if Amazon had not forced his hand.
Welty and his partner had built a world-class e-commerce fulfillment facility, Quiet Logistics, by deploying robots sold by Kiva Systems.
In a typical warehouse, workers spend about three-quarters of their time walking the aisles and only one-quarter of their time picking goods from shelves. At Quiet Logistics, the Kiva robots, which looked like large orange step stools with wheels, zipped down the aisles, slipped under 1,000-pound shelves, locked and lifted them, and delivered the shelves to the packing tables. Once there, lights on the shelves showed workers which products to pack.
“You almost couldn’t make a mistake,” Welty said. And by eliminating time wasted by walking to a shelf, Kiva helped Quiet Logistics fulfill orders with only a fraction of the usual workforce.
Welty and his partner were more than warehouse operators—they had previously run a business building warehouse management systems to monitor and organize the flow of products through the warehouse. Linking their system with Kiva’s software made the robot even smarter and dramatically improved warehouse throughput.
Welty became a Kiva evangelist, and Kiva brought potential customers to his warehouse. One group came from Amazon, the world’s largest operator of e-commerce warehouses. Amazon came away so impressed, it bought Kiva for $775 million in the summer of 2012.
The next year, Amazon would use all future Kivas in its own warehouse.
“We couldn’t operate without robots,” Welty said. “We needed the cost savings.”
Welty traveled to other robot companies with warehouse initiatives, but came back thoroughly unimpressed.
“They had robots that could work in a warehouse,” Welty recalled. “But if we helped them build a warehouse robot, they would end up with a really valuable company that someone else would buy. It was stupid to take the risk.
“We thought about it and decided that building our own robot was not that difficult to do.”
That’s how Welty and his partner founded Locus Robotics, based in Wilmington, Mass.
Locus is just one of dozens of startups trying to conquer the warehouse market. Some, like Fetch Robotics, 6 River Systems, and Plus One Robotics, have pedigrees with the leaders in the robotics field. But others are outsiders. Indianapolis-based Bastian Solutions is a materials automation company. Autonomous Shelf, founded in Shanghai, coded warehouse software. Austria’s Knapp makes sophisticated conveyor systems. Swisslog builds conveyors and warehouse software.
Warehouse companies that don’t figure out how to compete against Amazon and its fleet of 45,000 to 50,000 robots won’t survive long. And with Amazon holding onto its Kiva robots, these robot startups have a ready market. Thankfully for them, the rapid emergence of a supply chain of sensors, hardware, and software, plus a talented engineering workforce makes building autonomous mobile robots easier than ever.
So, while driverless cars make front-page news, the more controlled environment of the warehouse has made it the ground zero for commercial autonomous robots—and a showcase for how engineers will develop and integrate smart robots in the future.
;custompagebreak;Automating Warehouse Operations
Warehouses used to be the hub of a relatively simple logistics operation. They received and stored pallets of identical goods from manufacturers and importers, and then sent boxes via a conveyor belt or cart to trucks destined for retail outlets. Walmart combined sales monitoring and automatic replenishment to perfect this model and dominated American retail in the 1990s.
Over the past 15 years, however, warehouses have undergone a revolution. The economics of loading entire boxes onto a truck bound for a single destination broke down when online orders from consumers required opening the boxes, fishing out a single item, and then bundling just two or three items into a shipment to a home address.
“There were lots of shakeouts all the time,” Welty said. “It was hard to track a million items, and every time someone stored something in the wrong location, it led to another error in shipping. It was expensive to manage and hard to make money.”
Automating warehouse operations via Kiva robots was a way to bring down costs and improve quality control. Connecting warehouse software with Kiva’s control system enabled warehouse operators to reconcile deliveries, orders, and shipments on the fly without ever shutting down to count inventory. The system would constantly rearrange shelves to place the most popular items closest to packers, and could store popular items in several locations, so it had more ways to deliver products quickly or supply the same product to several packers at a time.
Kiva warehouses make storage robot-only areas to keep humans away from half-ton moving shelves. Because there is no human or forklift traffic, operators can place shelves closer together and squeeze up to 25 percent more storage into the same area. The robot section needs no heat or light. There is also much less opportunity for theft.
Welty loved Kiva's advantages, but after four years he also saw its flaws. To find locations, Kiva required thousands of bar-coded floor stickers that had to be maintained. When things fell off shelves, workers had to enter the robot-only area to retrieve them. Kiva’s infrared sensors did not always prevent serious accidents, and units grounded to a stop when dust and grime clogged their exposed drives.
While Kiva cost much less than a sophisticated conveyor system, it was still expensive. Welty, for example, spent more than $10 million and had to configure his entire warehouse to use it.
Welty had few doubts he could build a robot that could address those flaws. Starting with mainframe software in the 1970s, he had spent his career on the leading edge of technology. He was based in the Boston area, a hotbed of robot technology, and knew many of the players from lectures, meetings, and lab visits.
In fact, by 2012 it was growing much easier to build autonomous robots by integrating proven mechanical components, sensors, and software into a smart system, said Kostas Bekris, an associate professor of computer science at Rutgers University.
One of the key breakthroughs was improved AI systems for vision, Bekris said. Not only have sensors improved and come down in price, but engineers have become more proficient in fusing data from different types of sensor systems into usable 3-D images. Better vision systems enable robots to navigate a busy warehouse while avoiding collisions.
Technologists can also draw on a vast array of software, including the industrial version of the open-source robot operating system, ROS-Industrial. Other programs help process sensory data, map environments, and find locations.
Despite these advances, robots cannot do everything. They may be able to wheel down the aisles and find the right bin, but once they get there, they are less effective than a human.
“Think of a fulfillment center and the tens of thousands of different items on the shelves,” said Erik Nieves, who spent 25 years at Yaskawa before starting his company Plus One Robotics. “What makes a human so successful in that environment?”
Nieves says humans outpace robots when it comes to vision and grasping ability. Humans are also able to think on their feet. “Put a promotional logo on a pack of batteries and the vision system may no longer recognize it,” he said.
Some of these issues are problems that won’t be solved for a generation, Nieves says, so his company is addressing only the parts that can be tackled with today’s technology. Other robot developers have come to a similar conclusion. Their robots, which are just reaching warehouses now, not only look and work differently than Kiva’
;custompagebreak;Imaging the Environment
Next-generation robots have master control systems to optimize their movements, as do the Kiva robots. But these new robots are designed to collaborate with human workers rather than banishing them from the aisles, which means the robots must move briskly across the warehouse floor while avoiding people, forklifts, pallets, and boxes. They must identify blocked passages to plan alternate routes, and communicate with workers when they reach their destination.
To do these things quickly, robots must be smart enough to make these decisions while moving up to 2 meters/second.
That starts with sensors that image the environment and help avoid collisions. Most robot startups base their vision system on LIDAR, which scans its environment 20 times a second with a laser beam to produce a 3-D image.
Chuck, the robot built by 6 River Systems, uses an off-the-shelf LIDAR that costs about $800 and sees 25 m. LIDAR works well for obstacle avoidance, but Chuck uses it only to scan the 6 in. closest to the floor. Jerome Dubois, cofounder of 6 River, said, “If a person stands in front of it, it sees feet and legs but may think this is a rack and cut the corner instead of slowing down and take a wider route around.”
To help Chuck make safer decisions, 6 River incorporates a second vision system, a 3-D camera like those found on Microsoft Kinect. That system flashes a grid of dots onto the environment and measures their spread to assess distance.
Melonee Wise, CEO of Fetch Robotics, combines LIDAR with a time-of-flight 3-D camera. Instead of shining a grid of dots, it flashes a blast of infrared light and times the reflections to measure distance. She says it is more reliable than other 3-D cameras, which may have problems with sunlight or bright lights. It also images “difficult” objects, like forklifts with their tines in the air. The cameras have a range of 5 to 15 m and cost from $500 to $1,500.
Vision systems also enable robots to map the warehouse as they roll across the floor. Customers can then “paint” the map to define permanent features like racks, packing areas, loading docks, and battery recharging stations. They may also add preferred robot lanes, one-way aisles, and places where robots should queue while awaiting assignment. Users then use this logical map to promulgate the rules of the road. They might, for example, tell robots to slow down in high-traffic areas or sound warning beeps when making turns.
The robots update the map continuously, Dubois added. “If a robot sees a pallet on the ground, it adds it to the map,” he said. “Then every other robot in the warehouse knows it is there and plans accordingly.”
To avoid obstacles or find the fastest path to a pick, robots must know their precise location. Kiva’s floor barcodes work well on predefined routes, but they are too difficult to install and maintain when robots have free run of the entire warehouse. Most autonomous robots orient themselves using warehouse Wi-Fi networks, but technologists must also design robots to move safely in dead zones with little or no Wi-Fi reception.
Proving Grounds
The next generation warehouse robots have more in common than sensors and software. They also behave similarly. Unlike Kiva, which brought products to people, these robots improve productivity by shuttling products between pickers and packers.
They also help workers find their picks and reduce errors. For instance, 6 River’s Chuck rolls down the aisle to the target shelf and shines a light to show where the bin is located. Most robots also have display screens to show the product and quantity, and built-in scanners to confirm the worker fulfilled the order correctly.
A single robot might pick up parts of different orders from several nearby aisles.
“Chuck might come back with 12 different orders in two bins,” Dubois said. “It might drop off three orders at the UPS express pack station, and three more for gift wrapping. The rest go to another station. The display shows workers at each station what to grab. Normally, a warehouse would sort these combined orders with combination of conveyors, diverts, and chutes. With a mobile robot, you get the sorting for free.”
Even so, Dubois freely admits that Chuck is not as efficient as Kiva’s rolling shelves. But 6 River’s system does cut walking time by at least half, and operators do not have to rebuild their warehouse to deploy it. Chuck also costs less. Dubois, a former Kiva executive, estimates that a Kiva system cost $500,000 per packing station, compared with $60,000 for Chuck, including hardware and software.
Most warehouses that purchase these next-generation robot systems will pay back the investment in 18 to 24 months. Locus, Fetch, and other companies make similar claims. In fact, Fetch offers a stripped-down system that can pay for itself within two or three months, Wise said.
These next-generation robots also boost throughput and reduce errors and theft, all with a smaller workforce. These economics are impossible to ignore, especially when Amazon is showing how they drive business efficiency.
Economics make warehouses a great proving ground for autonomous robots. The need is there, and the environment is challenging. Although warehouses are controlled environments, they are filled with changing obstacles, traffic, and unexpected surprises. Unlike driverless cars on a roadway, warehouse movements are slow enough—less than 5 mph, rather than 50—for today’s autonomous technology to process images and make decisions about movements. That means warehouse robots, unlike self-driving cars, can operate without a technician onboard who can take over in an emergency.
So, think of warehouses as labs for autonomy, a way to test the emerging supply chain of sensors, hardware, software, and machine learning tools that make autonomy possible.
Today’s warehouses are just the beginning. From them will spring the proven technologies that will eventually bring autonomous robots to factories, hospitals, malls, city streets, and eventually high-speed roadways.