Bolstering Batteries with Zinc
Bolstering Batteries with Zinc
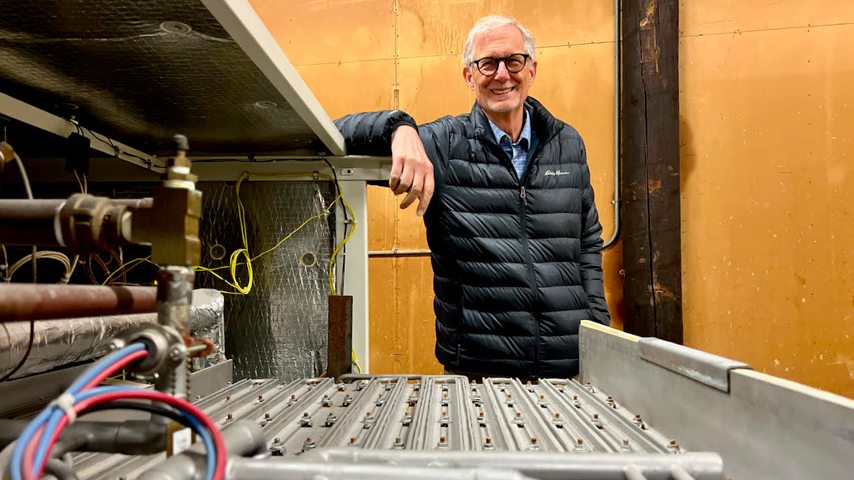
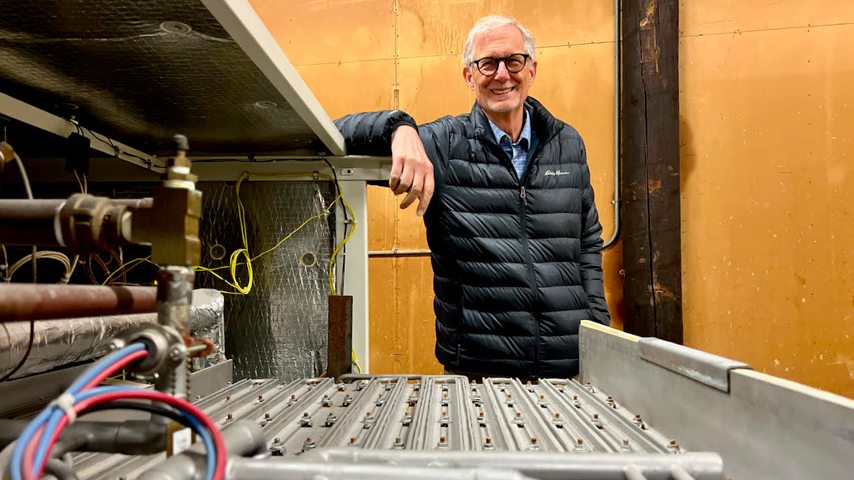
Enzinc’s Michael Burz is working to improve existing batteries with zinc.
Zinc, the material commonly used to power small button and hearing aid batteries, is getting a closer look. It’s inexpensive, readily available, and safe to use, which makes it an attractive choice to complement popular lithium-ion batteries.
The U.S. Navy, for one, had been looking for efficient alternatives to the lead-acid batteries currently used aboard ships and submarines, said Michael Burz, co-founder and president of Enzinc, a Richmond, Calif.-based manufacturer of zinc-based batteries. The Navy’s first attempt evaluated lithium, but the element does not work well in saltwater. The search was on to find a battery that could deliver the energy of lithium but was as safe and robust as the lead-acid batteries they were using.
Enter zinc. In the search for the best zinc battery, the zinc-air battery is the ultimate goal.
“A high-performance metal-air battery is considered the holy grail of batteries because it’s simple, low-cost, safe, and recyclable,” Burz said.
Become a Member: How to Join ASME
Unfortunately in the case of zinc, the zinc-air solutions are not easy because oxidation and reduction within the same structure is difficult to facilitate. A few zinc-air carbon batteries candidates simply place zinc in the middle, with oxidation occurring on one side and reduction on the other. Such a solution may work, but “You end up with a much lower specific energy and energy density because you’re not really taking advantage of the structure,” Burz said. A bifunctional cathode that can do oxidation and reduction in the same structure is the goal.
Zinc as the anode coupled with a number of cathode materials can do the job and are being test-driven as alternatives. Enzinc is on its way to developing a zinc-air battery where the cathode is simply air, but it’s starting first with a nickel cathode. Working with nickel, a well-characterized and familiar cathode, will help accelerate the product to market. Equally important, it will shine the spotlight on the zinc anode, Burz said.
A zinc anode battery might be a strong contender but it suffers from a significant disadvantage that also plagues batteries of other kinds: The batteries don’t last through many operational cycles because they tend to short out.
Conventional zinc batteries are made with zinc powder suspended in an electroconductive paste. When the battery is operational the zinc converts to zinc oxide, which when recharged is theoretically supposed to convert back to zinc. Unfortunately, not all the zinc oxide converts back and instead forms whisker-like dendrites that obstruct flow of current. Over time, the channels through which the current can flow become increasingly narrow. As the pathways get smaller, the impedance rises, and hot spots and dendrites grow rapidly, eventually leading to short circuits.
More for You: Sodium-ion Batteries Are Ramping Up
A lot of work in the area has focused on preventing the formation of harmful cycle life-limiting dendrites. Additives are one common route. Enzinc’s solution is to create a zinc metal sponge structure, which Burz said confers a host of advantages.
First, the zinc oxide forms only on the external surface of the sponge, leaving an interior core of pure zinc metal. “There’s always a pathway for the current to flow with no hot spots or dendrite growth,” he said.
The sponge-like zinc battery structure that Enzinc is working on has a high surface area and delivers 130 Watt hours/kilogram, twice the energy density of lithium-iron-phosphate or other equivalent zinc batteries.
Finally, the structural solution means it doesn’t need additives, Burz pointed out. “It’s a platform solution so we can couple this with nickel, manganese or silver, or with carbon for a zinc-air battery,” he said. “Instead of using very expensive or exotic materials in a conventional structure, we’re using a common material in a unique structure. So when we talk about high-performance, this is something that can compete with lithium batteries in the marketplace.”
Editor's Pick: Taming Sodium Hydroxide for Energy Storage
The applications for the range of zinc batteries are enticing. “Imagine if you have a zinc-air battery that is actually built into the wing and the fuselage of an electric drone. You can have economically viable long-range electric aircraft,” Burz said. Any applications where the battery can be engineered for curved surfaces and which require high energy density are good applications, he added.
Most of the world is looking for electric vehicles and batteries that won’t cost a lot of money, won’t catch on fire, and can be recycled, Burz noted. For now, the zinc batteries being developed are expected to fit into legacy lead-acid structures.
“You substitute the lead plates, you put in either zinc-nickel or zinc-manganese using the exact same battery housing and equipment within that factory, and you have a high-performance battery,” Burz said. “What that means is that we can triple the capacity using existing manufacturing infrastructure to provide a battery equivalent to lithium-iron phosphate.
Poornima Apte is a technology writer in Walpole, Mass.
The U.S. Navy, for one, had been looking for efficient alternatives to the lead-acid batteries currently used aboard ships and submarines, said Michael Burz, co-founder and president of Enzinc, a Richmond, Calif.-based manufacturer of zinc-based batteries. The Navy’s first attempt evaluated lithium, but the element does not work well in saltwater. The search was on to find a battery that could deliver the energy of lithium but was as safe and robust as the lead-acid batteries they were using.
Enter zinc. In the search for the best zinc battery, the zinc-air battery is the ultimate goal.
“A high-performance metal-air battery is considered the holy grail of batteries because it’s simple, low-cost, safe, and recyclable,” Burz said.
Become a Member: How to Join ASME
Unfortunately in the case of zinc, the zinc-air solutions are not easy because oxidation and reduction within the same structure is difficult to facilitate. A few zinc-air carbon batteries candidates simply place zinc in the middle, with oxidation occurring on one side and reduction on the other. Such a solution may work, but “You end up with a much lower specific energy and energy density because you’re not really taking advantage of the structure,” Burz said. A bifunctional cathode that can do oxidation and reduction in the same structure is the goal.
Zinc as the anode coupled with a number of cathode materials can do the job and are being test-driven as alternatives. Enzinc is on its way to developing a zinc-air battery where the cathode is simply air, but it’s starting first with a nickel cathode. Working with nickel, a well-characterized and familiar cathode, will help accelerate the product to market. Equally important, it will shine the spotlight on the zinc anode, Burz said.
A zinc anode battery might be a strong contender but it suffers from a significant disadvantage that also plagues batteries of other kinds: The batteries don’t last through many operational cycles because they tend to short out.
Conventional zinc batteries are made with zinc powder suspended in an electroconductive paste. When the battery is operational the zinc converts to zinc oxide, which when recharged is theoretically supposed to convert back to zinc. Unfortunately, not all the zinc oxide converts back and instead forms whisker-like dendrites that obstruct flow of current. Over time, the channels through which the current can flow become increasingly narrow. As the pathways get smaller, the impedance rises, and hot spots and dendrites grow rapidly, eventually leading to short circuits.
More for You: Sodium-ion Batteries Are Ramping Up
A lot of work in the area has focused on preventing the formation of harmful cycle life-limiting dendrites. Additives are one common route. Enzinc’s solution is to create a zinc metal sponge structure, which Burz said confers a host of advantages.
First, the zinc oxide forms only on the external surface of the sponge, leaving an interior core of pure zinc metal. “There’s always a pathway for the current to flow with no hot spots or dendrite growth,” he said.
The sponge-like zinc battery structure that Enzinc is working on has a high surface area and delivers 130 Watt hours/kilogram, twice the energy density of lithium-iron-phosphate or other equivalent zinc batteries.
Finally, the structural solution means it doesn’t need additives, Burz pointed out. “It’s a platform solution so we can couple this with nickel, manganese or silver, or with carbon for a zinc-air battery,” he said. “Instead of using very expensive or exotic materials in a conventional structure, we’re using a common material in a unique structure. So when we talk about high-performance, this is something that can compete with lithium batteries in the marketplace.”
Editor's Pick: Taming Sodium Hydroxide for Energy Storage
The applications for the range of zinc batteries are enticing. “Imagine if you have a zinc-air battery that is actually built into the wing and the fuselage of an electric drone. You can have economically viable long-range electric aircraft,” Burz said. Any applications where the battery can be engineered for curved surfaces and which require high energy density are good applications, he added.
Most of the world is looking for electric vehicles and batteries that won’t cost a lot of money, won’t catch on fire, and can be recycled, Burz noted. For now, the zinc batteries being developed are expected to fit into legacy lead-acid structures.
“You substitute the lead plates, you put in either zinc-nickel or zinc-manganese using the exact same battery housing and equipment within that factory, and you have a high-performance battery,” Burz said. “What that means is that we can triple the capacity using existing manufacturing infrastructure to provide a battery equivalent to lithium-iron phosphate.
Poornima Apte is a technology writer in Walpole, Mass.
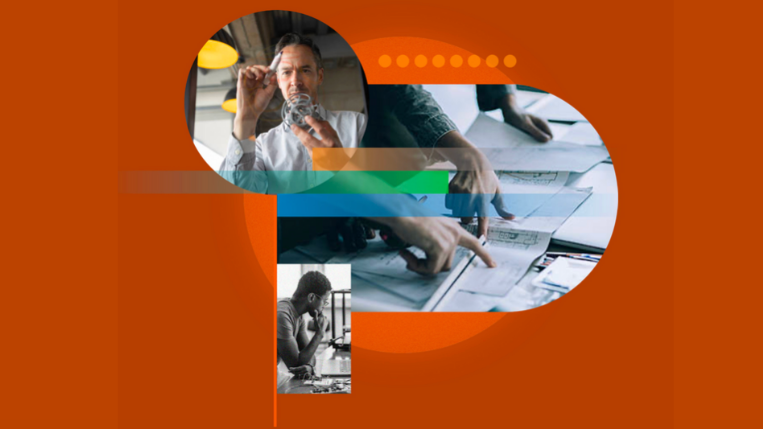
Pulse of the Profession: Design for Manufacturing
New technologies and ways of working give engineers full visibility into production processes and constraints.