6 Questions with Michael Grieves on the Future of Digital Twins
6 Questions with Michael Grieves on the Future of Digital Twins
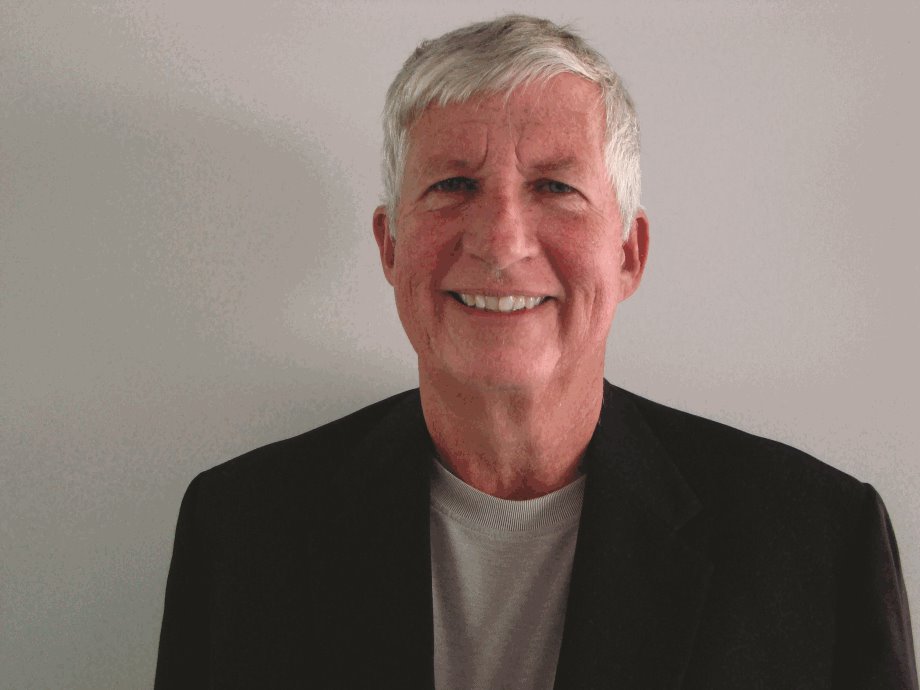
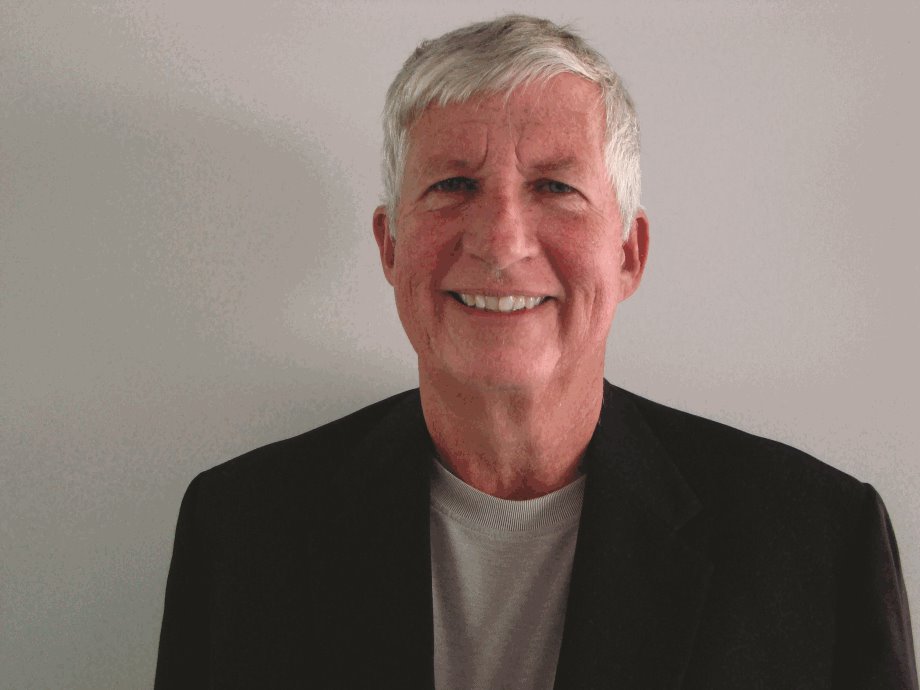
Michael Grieves originated the concept of the digital twin and at ASME’s Digital Twin Summit he discussed the future of the digital twin.
Michael Grieves, DBA/EDM, is the chief scientist of advanced manufacturing and the executive vice president of operations at the Florida Institute of Technology. There he helped form the Center for Advanced Manufacturing and Innovative Design. Grieves is best known for being an expert in product lifecycle management and the originator of the concept of the digital twin. He focuses on virtual product development, engineering, and manufacturing, mainly additive manufacturing and operational sustainment.
Q1: Your keynote at the ASME’s Digital Twin Summit covered intelligent digital twins, basically the layering of artificial intelligence and machine learning into today’s digital twin. How can we define the level of AI that’s found in today’s digital twin?
M.G: I think we could define it at level zero. There really isn’t much AI and in today’s digital twin, but it is fast approaching. Right now, my perception is we’re in the conceptual stage of digital twins. We have this information that we can bring together to create this virtual version of real-world environments based on models and behavioral aspects and modeling and simulation. The next step is to have all this information be pulled together automatically and intelligently, and we’re starting to see that occur as the software capabilities begin to arise.
Watch Our Latest Video: The Digital Twin World at Your Fingertips
Q2: Would it be fair to say that the engineer’s role in an advanced AI-driven digital twin is to be the decider of data sets?
M.G: Remember, as humans, our focus is goal orientation, but we always don’t minimize resources. AI can help us to reduce resources by advising us what won’t work or if it’s been tried before. It will serve as an augmentation to humans. Quite frankly, all the data being collected is overwhelming to humans. With that data, AI can organize and optimize our decision process by providing humans with the most reasonable engineering paths. Humans are too optimistic, and we tend to only look at data that confirms what we were thinking. I believe that that artificial intelligence can help us in that area.
Q3: What do you see are the future advances that will come with more AI features being married with a digital twin?
M.G: I expect that we’re going to start to see AI comb through massive amounts of information and do those computations that humans aren’t particularly good at. Being able to quantify and run multiple scenarios to help engineers make the best decisions. Again, we as humans get locked into a box sometimes in terms of our perspective. AI will help us determine what choices have a 98 percent probability of success versus a 75 percent probability of success.
Take Our Quiz: How Much of a Digital Engineer Are You?
Q4: How is that going to affect the manufacturing and production cycle?
M.G: The whole idea of being a factory foreman is once I get to perfection on the factory floor, I want every day to be exactly the same day. What the digital twin will be doing is looking for variations from that perfection and then giving us a heads up to go fix it. So, if a robot stutters and causes a slight delay, which will cause a bottleneck down the line, we’d like to know that before the bottleneck occurs.
Q5: What skill set should engineers be adopting or learning to better prepare for a future with digital twins?
M.G: Digital twins will also force engineers to be less siloed and require input from other people downstream. Having these integrated teams between will blur the barriers between departments and take engineers out of their comfort zones. They will need to know if a part is manufacturable, how it will perform prior to building, and change their design requirements and broaden their perspective. Educational institutions will have to have a broader view of what constitutes a successful product and how do I look at the different phases within its lifecycle.
Read the Robotics Blog: Digital Twins for Robot Installations
Q6: What are some ways that the industry can now prepare for implementing these digital twin strategies?
M.G: The industry first needs to recognize that this is where the trend is going. They will need to invest in digital tools to keep up. The second aspect is that for the major organizations to do it themselves. OEMs need to digitally integrate from the manufacturing floor and extend it down into the supply chain. Everyone needs to adopt these tools to stay current in the digital twin discussion.
Learn more at ASME’s Digital Twin Summit
Carlos M. González is special projects manager.
Q1: Your keynote at the ASME’s Digital Twin Summit covered intelligent digital twins, basically the layering of artificial intelligence and machine learning into today’s digital twin. How can we define the level of AI that’s found in today’s digital twin?
M.G: I think we could define it at level zero. There really isn’t much AI and in today’s digital twin, but it is fast approaching. Right now, my perception is we’re in the conceptual stage of digital twins. We have this information that we can bring together to create this virtual version of real-world environments based on models and behavioral aspects and modeling and simulation. The next step is to have all this information be pulled together automatically and intelligently, and we’re starting to see that occur as the software capabilities begin to arise.
Watch Our Latest Video: The Digital Twin World at Your Fingertips
Q2: Would it be fair to say that the engineer’s role in an advanced AI-driven digital twin is to be the decider of data sets?
M.G: Remember, as humans, our focus is goal orientation, but we always don’t minimize resources. AI can help us to reduce resources by advising us what won’t work or if it’s been tried before. It will serve as an augmentation to humans. Quite frankly, all the data being collected is overwhelming to humans. With that data, AI can organize and optimize our decision process by providing humans with the most reasonable engineering paths. Humans are too optimistic, and we tend to only look at data that confirms what we were thinking. I believe that that artificial intelligence can help us in that area.
Q3: What do you see are the future advances that will come with more AI features being married with a digital twin?
M.G: I expect that we’re going to start to see AI comb through massive amounts of information and do those computations that humans aren’t particularly good at. Being able to quantify and run multiple scenarios to help engineers make the best decisions. Again, we as humans get locked into a box sometimes in terms of our perspective. AI will help us determine what choices have a 98 percent probability of success versus a 75 percent probability of success.
Take Our Quiz: How Much of a Digital Engineer Are You?
Q4: How is that going to affect the manufacturing and production cycle?
M.G: The whole idea of being a factory foreman is once I get to perfection on the factory floor, I want every day to be exactly the same day. What the digital twin will be doing is looking for variations from that perfection and then giving us a heads up to go fix it. So, if a robot stutters and causes a slight delay, which will cause a bottleneck down the line, we’d like to know that before the bottleneck occurs.
Q5: What skill set should engineers be adopting or learning to better prepare for a future with digital twins?
M.G: Digital twins will also force engineers to be less siloed and require input from other people downstream. Having these integrated teams between will blur the barriers between departments and take engineers out of their comfort zones. They will need to know if a part is manufacturable, how it will perform prior to building, and change their design requirements and broaden their perspective. Educational institutions will have to have a broader view of what constitutes a successful product and how do I look at the different phases within its lifecycle.
Read the Robotics Blog: Digital Twins for Robot Installations
Q6: What are some ways that the industry can now prepare for implementing these digital twin strategies?
M.G: The industry first needs to recognize that this is where the trend is going. They will need to invest in digital tools to keep up. The second aspect is that for the major organizations to do it themselves. OEMs need to digitally integrate from the manufacturing floor and extend it down into the supply chain. Everyone needs to adopt these tools to stay current in the digital twin discussion.
Learn more at ASME’s Digital Twin Summit
Carlos M. González is special projects manager.