3D-Printed Ceramic Turbine Parts Withstand High Temperatures
3D-Printed Ceramic Turbine Parts Withstand High Temperatures


A research team 3D printed a gas turbine component using ceramic material, which can withstand higher temperatures than the conventional metals. Photo: Kate Myers/Penn State.
Ceramic materials have plenty of potential for improving the efficiency of gas turbine engines due to their high temperature tolerances. Although there is a fair amount of research on ceramic materials for gas turbines, these materials are still not commonly used because of the difficulty of fabrication (especially for complex shapes) and the challenges in withstanding such a high-stress environment.
To advance possible opportunities for using ceramics in super-hot applications such as gas turbines, a team of researchers at Pennsylvania State University decided to explore making ceramic components using a unique additive manufacturing (3D printing) process. The results were highly encouraging—the team created a component with complex internal cooling features that enabled it to withstand higher temperatures and therefore increase fuel efficiency.
“Our process is unique in that we generated complex-shaped parts very easily and very cheaply using this new approach,” said Steve Lynch, principal investigator and associate professor of mechanical engineering at Pennsylvania State University.
Innovating with additive
The research team—Lynch and other researchers from Penn State’s Materials Science and Engineering Department, the Colorado School of Mines, and the University of Wyoming—used this process to produce heat-resistant airfoils using a polymer-derived ceramic material.
Initially, the ceramic 3D printing method was inspired by a publication in Science (Eckel et al., 2016) that outlined a new potential manufacturing process. Prior to this article, all additive manufacturing of ceramics was done by burning off the binder material followed by sintering. “However, combining polymer-derived ceramics with 3D printing opened the door to a whole new manufacturing paradigm,” said Lynch. “After recognizing the impact of Eckel’s work and knowing that we had all the tools and know-how at our disposal, it was natural for us to move into this research space.”
Become a Member: How to Join ASME
The polymer-derived ceramics were created by firing a plastic-like base in a furnace. “We adapted that to create these turbine airfoils, but also leveraged the design freedom of additive manufacturing to create internal features that dramatically improve the effectiveness of the cooling air inside the blade,” said Lynch.
The researchers were able to create the exact shapes needed to withstand more heat and still perform well in the gas turbines. “We found that with the right design for the part, the ceramic airfoil shape that we 3D printed performed just as well as the metal components,” he added.
One of the biggest challenges for Lynch’s team was learning how to harness 3D printing technology with the new material system and the necessary post-printing steps to make reliable parts. In particular, the result from the 3D printing process—the solidified pre-ceramic polymer (the “green body”)—required pyrolysis at high temperature in an inert environment to become the final ceramic part. This process, though, causes shrinkage and some residual stresses in the final part, which must be addressed using an appropriate green body design.
“Another concern early on was perceived issues regarding our material design, but it turned out we were running into limitations with our printer hardware,” said Lynch. “Working with the manufacturer, we had to crack into the operating software to make it all work.
“Once this was understood, we then had to deal with nuances of new polymer resin recipes, interactions of 3D printing additives and the pre-ceramic polymer resins, and cracking of the parts during pyrolysis—all the usual issues experienced with experimental manufacturing studies.”
Surprises along the way
A benefit to Lynch’s approach was that the iterative process of finding the right materials, 3D-printing settings, and post-processing steps was fast and relatively inexpensive since the team was leveraging existing 3D printing technology and developments in pre-ceramic polymer resins. The team learned that making such a resin with all the appropriate properties (viscosity, reactivity, curing control) that could be 3D-printed with reliable and repeatable dimensional accuracy was also more challenging than they realized.
For Lynch, perhaps the best surprise was the truly multi-disciplinary aspect of the project: from materials science, to design, to manufacturing, to vane testing, to optimization modelling, and then all over again. “Since each of the team members was an expert in a particular area, we had to learn about each other’s field to ‘speak the same language,’” he said. “This probably was most beneficial for our graduate students who were immersed in this multi-disciplinary thinking from the start.”
More for You: 3D-Printed Copper Alloy Can Withstand 6,000 °F
Because of the design freedom of 3D printing, Lynch’s team did start to develop some optimization tools but “there is a lot more work to be done in this area, particularly to incorporate our new knowledge about the manufacturing process and the unique properties of ceramic materials relative to more conventional nickel superalloys that are prevalent in gas turbine engines,” he said.
With the general constraints on creating ceramics with complex geometries (difficulty in machining, cost, lead times), unlocking the ability to computer-generate and rapidly prototype parts that can withstand high temperatures “allows for a slew of possible applications,” said Lynch. In addition to turbine blades, heat- and chemical-resistant parts for a variety of applications can be generated.
An area where internally cooled ceramics might be useful is in hypersonic applications where the extreme speed of an aircraft (Mach 5 or greater) generates very high heating on the forward edges. Lynch’s method has the potential to be impactful in other fields as well that require parts with chemical inertness and high temperature resistance and high wear resistance.
Although this research project produced a completely new material system, manufacturing process, and design approach, Lynch cautions that, “while the results are exciting, it’s only just proof of concept. More research is needed to turn these results into the next turbine vane or equally useful product. To that end, we have started some new research extensions of this project to develop even more novel ways of 3D printing ceramics.”
Mark Crawford is technology writer in Corrales, N.M.
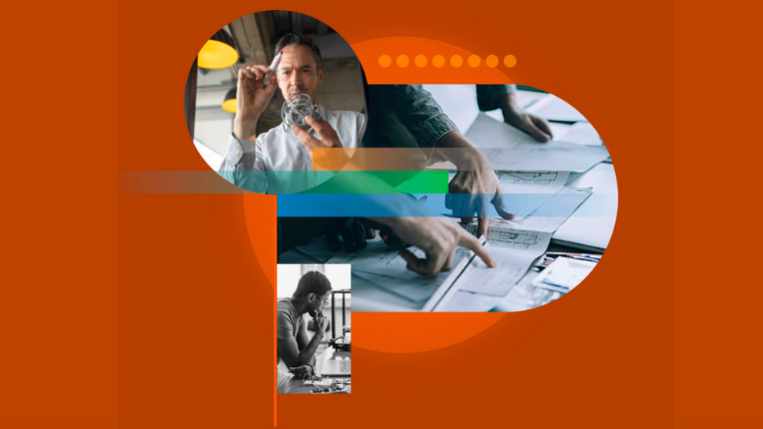