Six Lean Principles for an Industry 4.0 World
Six Lean Principles for an Industry 4.0 World
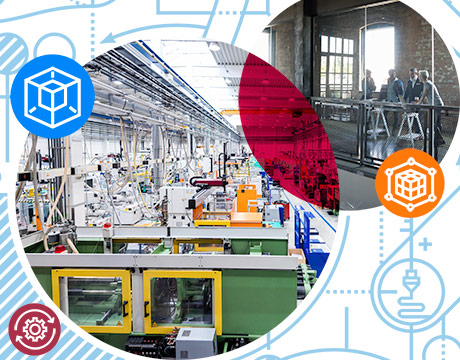
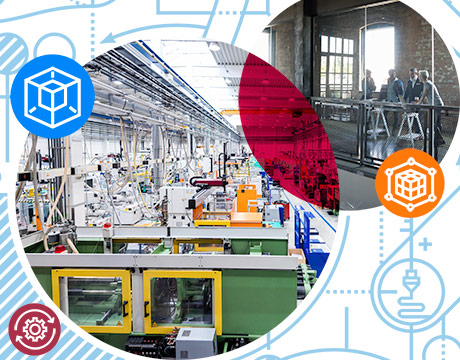
Lean manufacturing, a process that originated in Japan decades ago, is widely embraced by manufacturers today as a way to eliminate waste from manufacturing operations. “Lean” companies improve quality and efficiency through implementing core lean principles, thereby reducing cost, adding value for customers, and gaining a competitive edge in the marketplace.
Lean uses a number of tools that have changed little over the past 20 years. However, with recent technology advances, such as Industry 4.0 and the Internet of Things (IoT), lean goals can be achieved must faster. For example, value stream mapping—once a pen-and-paper exercise—is now available as a software package. Sensors, software, and real-time data have removed much of the guesswork from process optimization. As a result, lean itself is getting much leaner as these technologies evolve and are adopted on the manufacturing floor.
Editor’s Pick: The Rise from BattleBot to Corporate Robot
Even with new technologies, “lean is still about creating exceptional value for the customer,” said Jim Morgan, senior advisor for product and process developmentwith the Lean Enterprise Institute. “What is new is the growth in our understanding of how to apply lean principles, tools, and practices in new ways.”
Below are six of these top practices that can make engineers leaner in 2019.
1. Gemba
The first lean tool Morgan recommends is “gemba.” Gemba is a Japanese term for the “place where it happens.”
“Whether it is in the field with customers, the factory floor, or test facilities, engineers must get out of their cubes and conference rooms and spend time in the real world,” Morgan said. During a “gemba walk,” engineers simply observe the processes going on around them. “Tools are needed to capture what is learned during the gemba,” he said. “Notebook-and-pencil is my go-to tool, or sometimes a smart-phone camera.”
2. Obeya
Obeya is a Japanese word for “big room.” For lean purposes, this means a command center or project’s hub.
“This is where the cross-functional engineering team—manufacturing, supply chain, quality—works together collaboratively on a regular basis,” Morgan said. Visual management is key; walls are typically covered with up-to-date diagrams, figures, and data lists. “What matters most is that the space is inclusive, collaborative, safe, and transparent.”
Recommended: YouTube Star Goes Viral with Glitter Bomb
3. LPPD
Lean product and process development (LPPD) is essentially value stream mapping (VSM) on a much larger scale. VSM is the process by which a single value stream is analyzed, with wasted steps removed. LPPD focuses on creating value by doing VSM for the entire system—not just one process. “This means developing not only a product, but the product delivery system as well, including all the activities from raw materials to saleable goods,” Morgan said.
4. Cellular Manufacturing
Instead of relying on a standard production line to build a product in a sequence from receiving raw materials to the final inspection, cellular manufacturing builds parts in a dedicated cell of machines. Similar products or parts are grouped together so they can be manufactured in the same sequence and on the same equipment. This saves time by eliminating the changeover that would normally be required for different products.
5. 5S
5S (Sort, Straighten, Sweep, Standardize, and Sustain) is designed to keep a workplace safe, clean, and organized to save time and optimize efficiency. A very visual system, 5S optimizes work standardization efforts and productivity. For example, tools are always put away in the right place, materials and inventory are visible and accessible. A workplace organized according to 5S reduces mistakes and improves employee morale and productivity.
6. Poka Yoke
The goal of poka yoke is to eliminate mistakes before they happen—a core principle of lean. It is a proactive approach that can be applied to any process, at any time. Often, it occurs during design for manufacturability, or results from the implementation of other lean principles, such as VSM. When a potential problem is identified, a solution is found and put in place before production begins. IoT can be especially effective with poka yoke by analyzing machine performance and maintenance needs.
More on Industry 4.0: Manufacturing Takes Flight
Lean and Industry 4.0
With the advance of Industry 4.0 and the IoT, lean will become increasingly data-driven, to the point where these technologies are considered lean tools themselves. As attractive as this merging sounds, Morgan warned, it is a mistake to view this technology as a “silver bullet.”
“IoT is a powerful tool full of potential, but a tool nonetheless,” Morgan said. “IoT is making a huge impact on industries from healthcare to automotive to consumer electronics, but it does not replace the need for lean thinking and practice. In fact, it may make lean thinking more important than ever so that we stay focused on value creation. It is important to remain very intentional about the products and services we develop so that we don’t lose sight of our higher calling as engineers to help design and create a better world.”
Mark Crawford is an independent writer.
Read More Exclusive Content from ASME.org: Using the Eyes of Killer Shrimp to Design a Super Camera The Bionic Mushroom Tapping Signals Replacement for Keyboards
Lean itself is getting much leaner as Industry 4.0 and Internet of Things technologies evolve and are adapted on the manufacturing floor.Jim Morgan, Lean Enterprise Institute