Before You Design for Additive Manufacturing, Check Your Mindset
Before You Design for Additive Manufacturing, Check Your Mindset
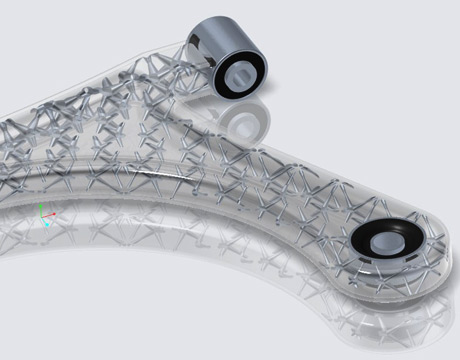
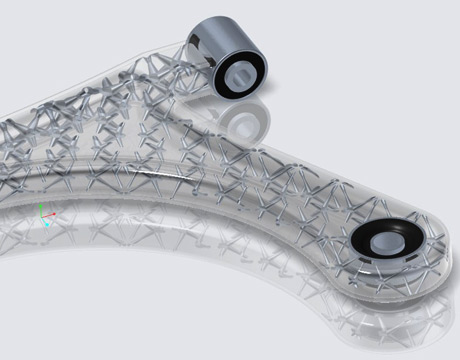
Content provided by PTC
Additive manufacturing (AM) promises faster time-to-market, reduced costs, and the ability to customize designs, whether you’re using AM for rapid prototyping or production.
Don’t make the mistake of thinking that what worked for traditional production will allow you to get the most from 3-D printing.
You must adopt a new mindset and come at common design problems differently.
The Constraints Have Changed
Without a ‘design for AM’ mindset, you might think about parts in a familiar way. The result? You limit your own creativity by accepting what’s possible using familiar production methods.
For example, undercuts, internal channels, even fillet placement matter with traditional manufacturing practice. But they don’t hold the same weight when you use 3-D printing technologies.
It’s understandable that you, especially if you’re seasoned, might struggle with such a mindset shift at first. Fortunately, advances in design software can offer various ways to rethink how you approach design problems. We feature three below.
Enter the Lattice
A lattice is a framework or structure of crossed strips and the resulting spaces between them. An optimized lattice structure promises greater strength with less material, which makes lattices especially useful for such products as lightweight structural panels, energy absorption devices, thermal insulation, or porous implants.
When you combine AM with generative design tools, it’s possible to get an optimized lattice structure you might never have considered. It gets even better: When you add a simulation product that’s tightly integrated with your CAD tool, you can test your design as you work before you make a single budget-sapping prototype.
Parts are the New Assemblies
AM can consolidate many parts into a single component, the implication being that a ‘design for AM’ mindset means reconsidering how you think about parts and assemblies.
In one famous example, GE redesigned its LEAP jet engine nozzle, reducing it from 18 separate components to a single part. GE achieved significant weight reduction and increased performance targets due to the streamlined shape and complex internal lattices. Or consider nature’s example—the human hip’s internal structure. What could you do if you decided to start small with this new mindset?
Embrace the Freedom of Generative Design
Don’t miss out on generative design tools and how they can help you capitalize on your engineering experience and judgement. With the Creo Topology Optimization Extension, you are the one who establishes the defined set of objectives and constraints, while the software determines the best design within the boundaries you’ve set and delivers B-Rep geometry. When you add the capabilities of AM, chances are that these designs are now within reach.
Making the Most of AM
Surely this is one of the most exciting times in our careers—new technologies, new goals, new ways of working. All of us are going to be asked to change. While AM technologies present a genuine opportunity, the experience of the seasoned engineer has never been more valuable. Now is the time to put the two together.
Learn more about design for additive manufacturing at ptc.com.